Technical expertise driving excellence.
Refusing a good tool to accept a bad one : it this a feasible solution ?
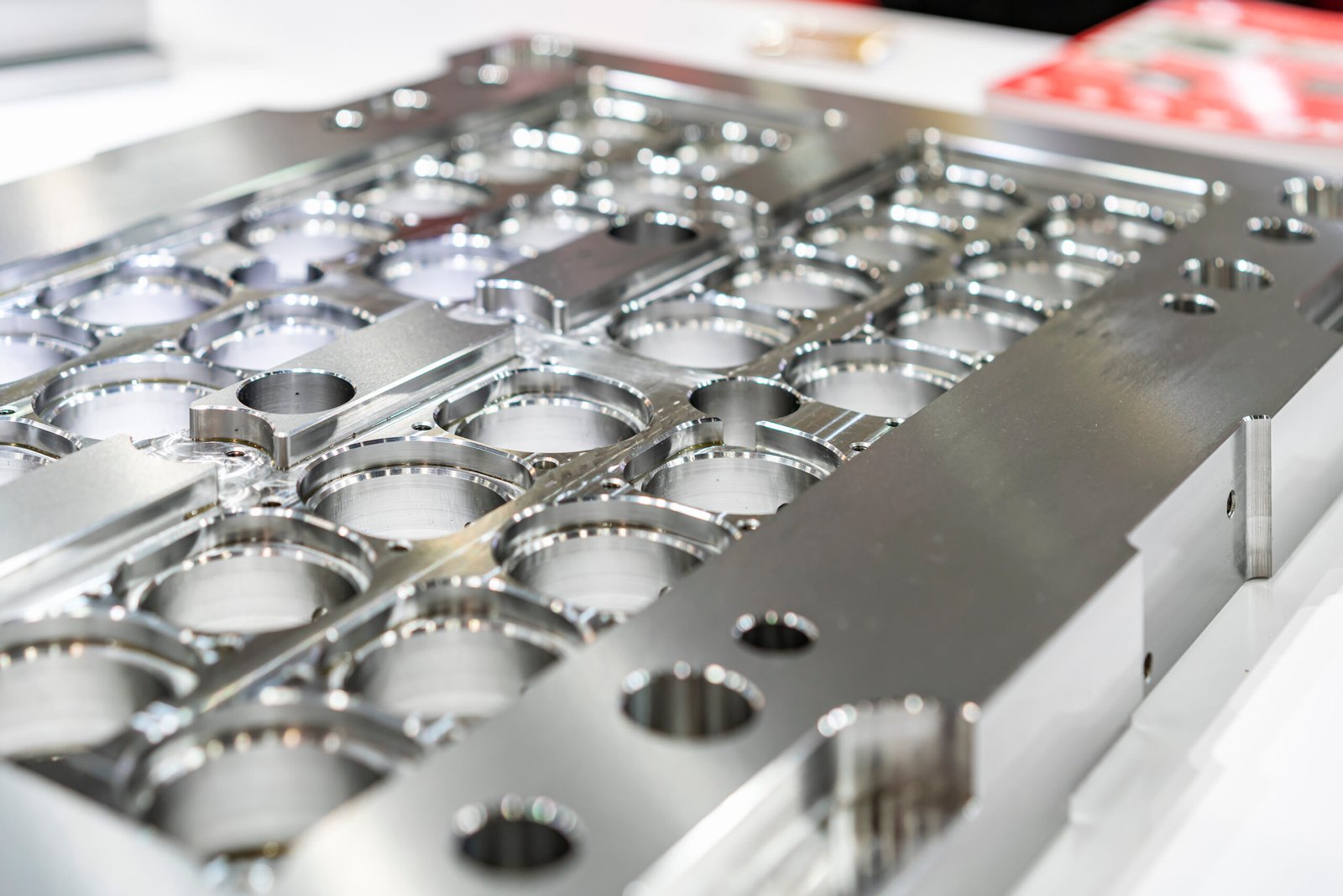
The validation phase of a series of component tooling is often associated as a set of independent sequential tasks.
If this consideration allows very simply the “distribution” of actions to different subcontractors, sometimes in different countries, it puts in the background the main objective of the robust design approach: will the product meet the user’s expectations?
The validation of production tools is a key moment in the project, which generally occurs very close to the date of market launch of your product, and therefore leaves very little room for modification or adjustment of a component.
Added to this is the potential complexity of tool modification (reworking, spindle modification, etc.), which can quickly lead to an out-of-control situation.
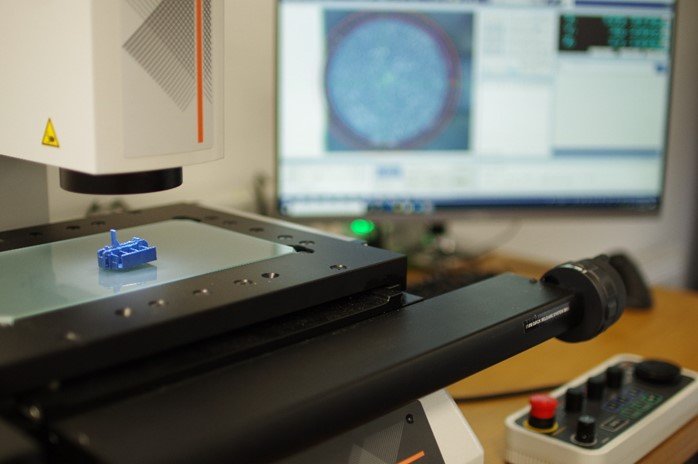
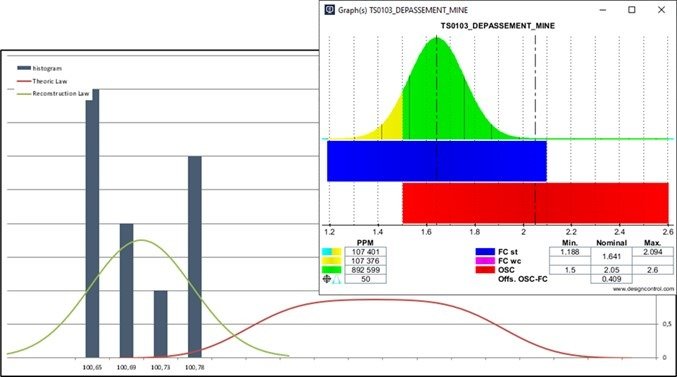
In reality, the acceptance of a tooling is a complex analysis which will verify the concordance of the part with the requirement of the drawing file, but also its compatibility with the other components and the final performance of the product. The systematic search for the best compromise for the product and the tooling guarantees that the business imperatives and time to market are met.
With this in mind, it is perfectly feasible to accept non-compliant tooling – the rejection or modification of which would be extremely costly – and to choose to modify another piece of compliant tooling in the series accordingly, while still meeting the functional requirements.
To achieve this objective, we have equipped our software with all the statistical tools necessary for process control and a qualification module that is essential for developing a high-performance tool validation at the lowest cost.
By linking Functional Analysis to FMEA and then to Technical Functional Analysis and its associated simulation models, Design Control Power has all the tools to develop a relevant control plan that minimizes the number of measurements while providing a probabilistic vision of the control of product functions.
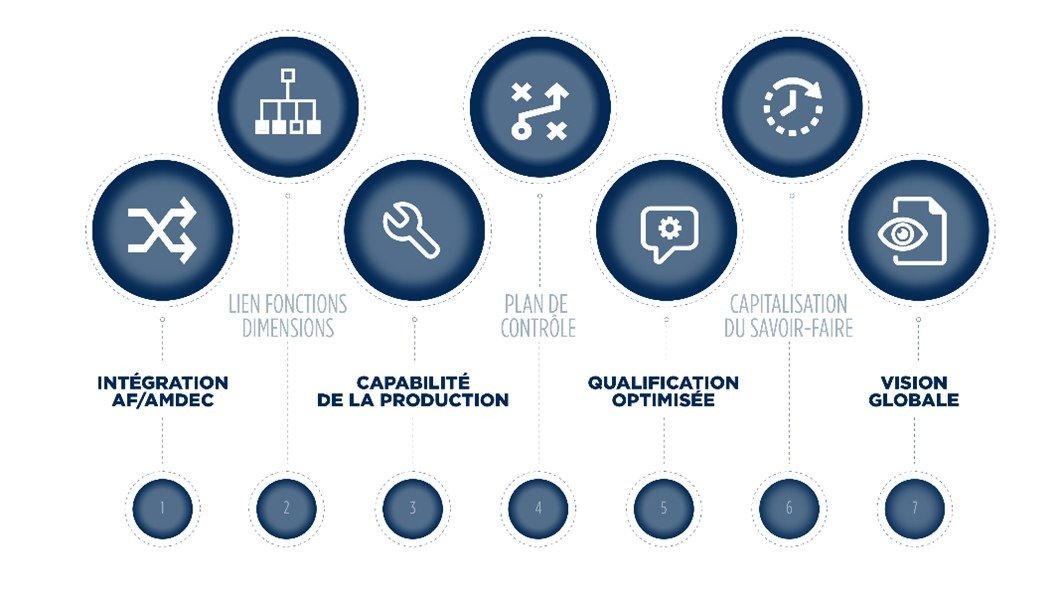
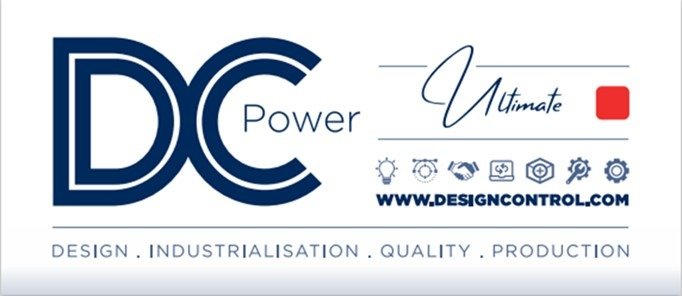
DCP has its own module to ensure the capability of the measurement in order to be able to fill in with confidence the measurement reports dedicated to the short-term validation of the functional and tooling parameters.
All the data collected will allow the user to simply evaluate the possibilities of acceptance of this manufacturing tool considered at first as non-conforming.
Design Control Power also has all the process aptitude tools (long term) and will allow an optimized implementation of the MSP follow-up.
You have doubts about the viability of this approach? You wish to learn more about the qualification methods used in our studies and tools? Do not hesitate to contact us.